この記事は 3 分で読めます
ジャストインタイムとは|コストを削減して販売機会を逃さない仕組み
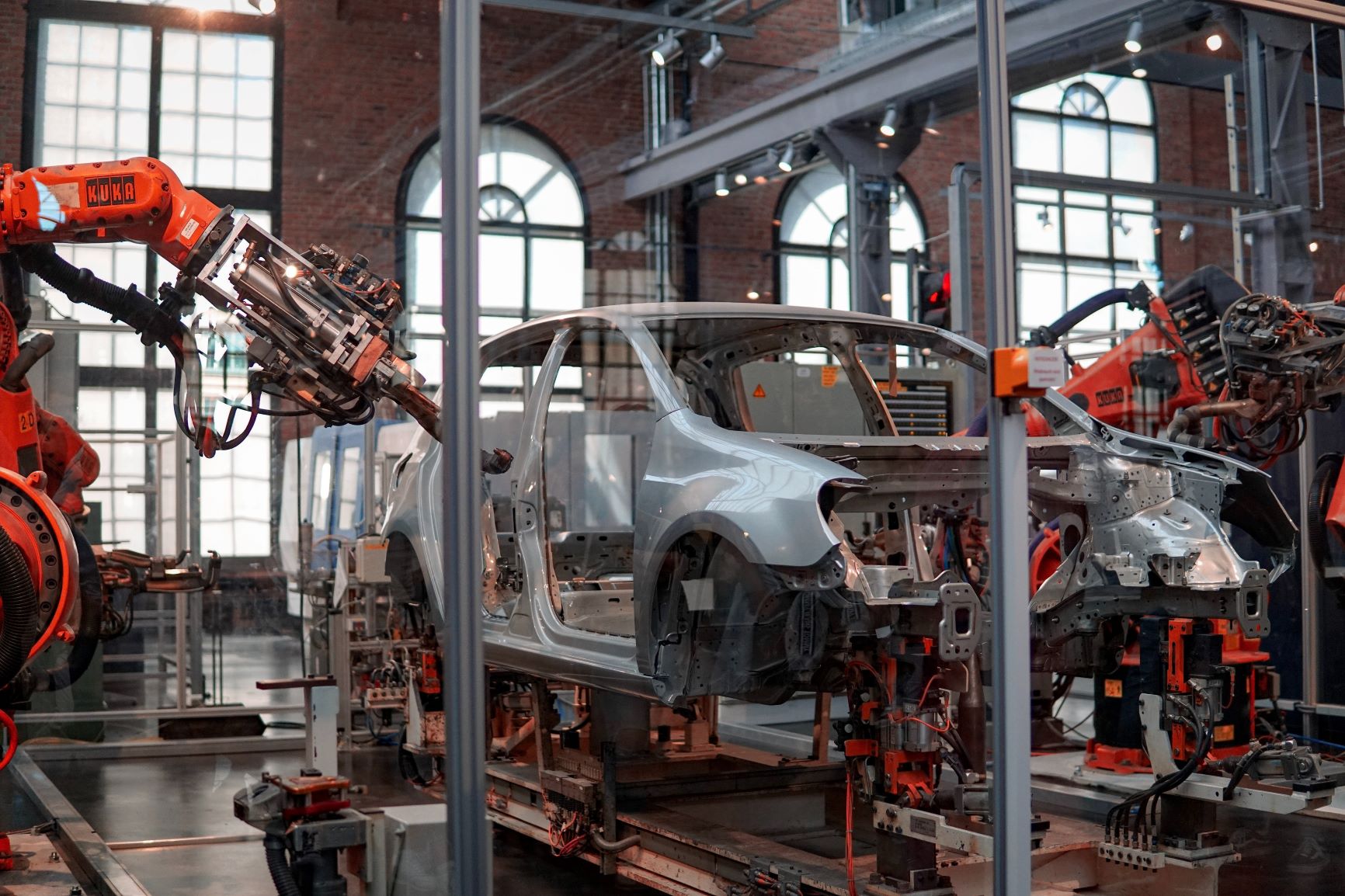
ジャストインタイムという言葉をご存じでしょうか?ジャストインタイムの仕組みを生産工程に組み込むことで、大幅なコストの削減を見込めますが、その一方でいくつかのリスクも伴います。
そこで今回は、ジャストタイムの仕組みとメリットに加えて、導入するときに注意すべきことも解説します。
目次
ジャストインタイムとは「必要なものを、必要なときに、必要なだけ供給する」考え方のこと
ジャストインタイムとは、「生産ラインの各工程ごとで無駄のない生産活動を行う」という考え方です。モノや人材、時間などを必要な場面で、必要なだけ使うことで効率的な生産活動を実現しています。
この考え方は、トヨタ自動車の創業者である豊田喜一郎氏によって考案されたものです。現在では、世界的にも有名で数多く導入されている仕組みであり、「JIT」で名が通っています。
「平準化生産」がジャストインタイムの大前提
平準化生産とは「製品(部品)の生産量・種類や、生産にかける時間を工程ごとに均等に振り分ける生産方式」です。例えば、ある工程で製品Aを1時間かけて100個生産するものを、A工程では10分で20個、B工程では20分で35個、C工程では30分かけて45個生産します。平準化生産が機能していることが、ジャストインタイムを導入するための前提となっています。
生産の最小単位(ロット)を定めて行う「ロット生産」では、タイミングで変わる必要な量ごとの生産へ切り替えることが難しく、必要な量だけを生産するジャストインタイムには対応できません。
一方、平準化生産を行えば、配置している人員や機械に応じて、生産量を適切に配分できるので無駄がなくなります。
ジャストインタイムの背景にある「自働化」と「かんばん方式」
ジャストインタイムを導入している生産工場では、機械の「自働化」と「かんばん方式」が行われています。
- 機械の自働化
機械が単に自動で動くだけでなく、問題やトラブルが生じれば自動で止まるよう制御されており、”自分で働く”ことから人偏の付いた「働」が使われています。もし、自動で止まる機能が無ければ、不良品を量産してしまうなどの事態に陥りかねません。 - かんばん方式
ジャストインタイムを導入した工場では、後工程が必要なものを必要なだけ生産するように前工程に伝え、前工程は伝えられたようにモノを製造します。そして、このやりとりをスムーズに行うために「かんばん」と呼ばれるカードが用いられます。
ジャストインタイムを成り立たせる三原則
後工程引取方式
後工程引取方式とは「生産ラインにおいて、後工程が必要なものを必要なだけ前工程から引き取り、前工程は引き取られた分だけ再度製造する生産方式」です。その取引を記録・管理するものとして、前工程で「仕掛けかんばん」を、後工程で「引取りかんばん」を使用します。かんばんを用いた後工程引取方式は以下の流れで行われます。
仕掛けかんばんの流れ
- 仕掛けかんばんに指示されている数だけ部品を製造します。
- 仕掛けかんばんを製品に貼り付け、置き場に運びます。
- 製品が後工程に引き取られると、仕掛けかんばんが外れます。(①に戻る)
引取りかんばんの流れ
- 前工程から支給された製品を受け取る際に、仕掛けかんばんを外し、引取りかんばんを付けます。
- 引取りかんばんが付いた製品を後工程に運びます。
- 製品が後工程に引き渡されると引取りかんばんが外れます。
- 引取りかんばんを持って置き場へ行きます。(①に戻る)
工程の流れ化
工程の流れ化とは「前工程と後工程との間で、余分な在庫や待ち時間が存在せず、スムーズに製品の受け渡しが行われるように取り組むこと」を言います。工程の流れ化が行われていれば、別の製品を後工程から依頼されても即座に対応することができます。その結果、さまざまな種類の製品を同じ工程で製造することが可能になります。
タクトタイムの調整
タクトタイムとは「製品の生産にかける平均作業時間」です。販売機会を失わないことや、在庫超過を招かないことを心掛けるためには、必要な生産数に応じた適切なタクトタイムを設定しなければなりません。
タクトタイムを長くしすぎると、急速に変化するニーズに対応できず、販売機会を失ってしまう危険性があります。また、タクトタイムを短くすれば生産にかかる人件費の費用対効果を高めることができますが、過度の短縮は在庫超過を引き起こしかねません。
ジャストインタイムで得られるメリット
在庫量を減らすことによるコストの削減
かんばん方式を取り入れたジャストインタイムでは、かんばんが回ってくるまでモノを発注・生産しないので、在庫量を減らすことができます。在庫量が削減されれば、保管するためのエネルギーを節約できることに加え、人件費も抑えられます。また、在庫超過を起こして原料を無駄にするリスクも減ります。
リードタイム短縮による販売機会の確保
リードタイムとは「商品の発注から納品までの全行程にかかる時間の総和」です。販売機会を逃さないためには、リードタイムを短縮するために一定数の在庫を常に用意しておかなければなりませんが、在庫管理には莫大なコストがかかります。一方、在庫を全く持たない完全受注生産では、発注されてから調達・生産にとりかかるので、リードタイムが長くなり販売機会を逃してしまいかねません。
しかし、ジャストインタイムでは、後工程から受注されるとすぐに生産に取りかかるため、在庫量を最小化した上でリードタイムを短縮でき、販売機会を失うリスクも減らせます。
ジャストインタイムで注意すべきこと
システム導入にコストがかかる
ジャストインタイムを導入するには、かんばん方式を導入したり、平準化生産を安定化させたりしなければなりません。工程間における情報管理・伝達のシステムを確立させることや、各工程で多種類の製品を作るための資源を準備することには時間やコストがかかってしまいます。また、工程の流れ化を実現することには、現場の慣れも必要になります。
在庫切れのリスクが伴うため、品質管理が重要である
ジャストインタイムでは、在庫を最小にしている分、在庫切れのリスクを伴います。もし、品質が悪化した場合、分析・改善などを行うために、生産ラインの一部を止めることになる可能性があります。それに加え、在庫も尽きると部品が足りなくなり、製品を完成できなくなってしまうことがあります。そのため、生産ラインを滞りなく機能させるには、品質管理を十分に行わなければなりません。
いかがでしたか?
ジャストインタイムでは、必要なものを必要なだけ生産して在庫超過を防ぐことができます。また、後工程からの受注ですぐに生産に取りかかるため、販売機会を逃しにくいメリットもあります。一方、ジャストインタイムを導入するには、平準化生産ができているといった前提が必要なので、自社の予算を加味して慎重に考えましょう。


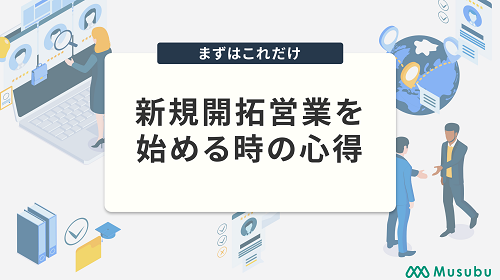

まずはこれだけ。新規開拓営業を始める時の心得
無料でダウンロードするために
以下のフォーム項目にご入力くださいませ。